Le leader européen de l’hébergement élabore et assemble lui-même ses équipements dans une usine que nous avons pu visiter près de son siège de Roubaix. 80 000 serveurs en sortent chaque année.
Six petits kilomètres séparent le siège d’OVH Cloud à Roubaix de son usine de Croix dans le Nord de la France. Le poids lourd européen de l’hébergement et du cloud y produit les serveurs qui viendront alimenter principalement sa quinzaine de data centers en Europe. Bien sûr, les composants viennent de l’étranger. Mais la conception et l’assemblage sont réalisés sur place. Un made in France que la société a beau jeu de mettre en avant en pleine crise mondiale d’approvisionnement. Sans compter que cela lui garantit une réactivité à toute épreuve pour alimenter ses huit centres de données implantés à Roubaix.
Rien ne se perd, tout se transforme
Il ne s’agit pas d’un petit atelier artisanal, mais d’une vaste installation avec une logique industrielle, qui permet de sortir 80 000 serveurs chaque année. Ici, rien ne se perd. 35% des serveurs sont conçus avec au moins un composant reconditionné récupéré dans le parc même d’OVH Cloud. Et 900 serveurs reviennent chaque semaine dans l’usine.
«Ils ont trois vies de chacune trois ans en moyenne. Ils voyagent dans différentes gammes, les clients n’ayant pas tous besoin des dernières générations de CPU », nous explique Dominique Michiels, Chief Service Delivery Officer d’OVH Cloud.
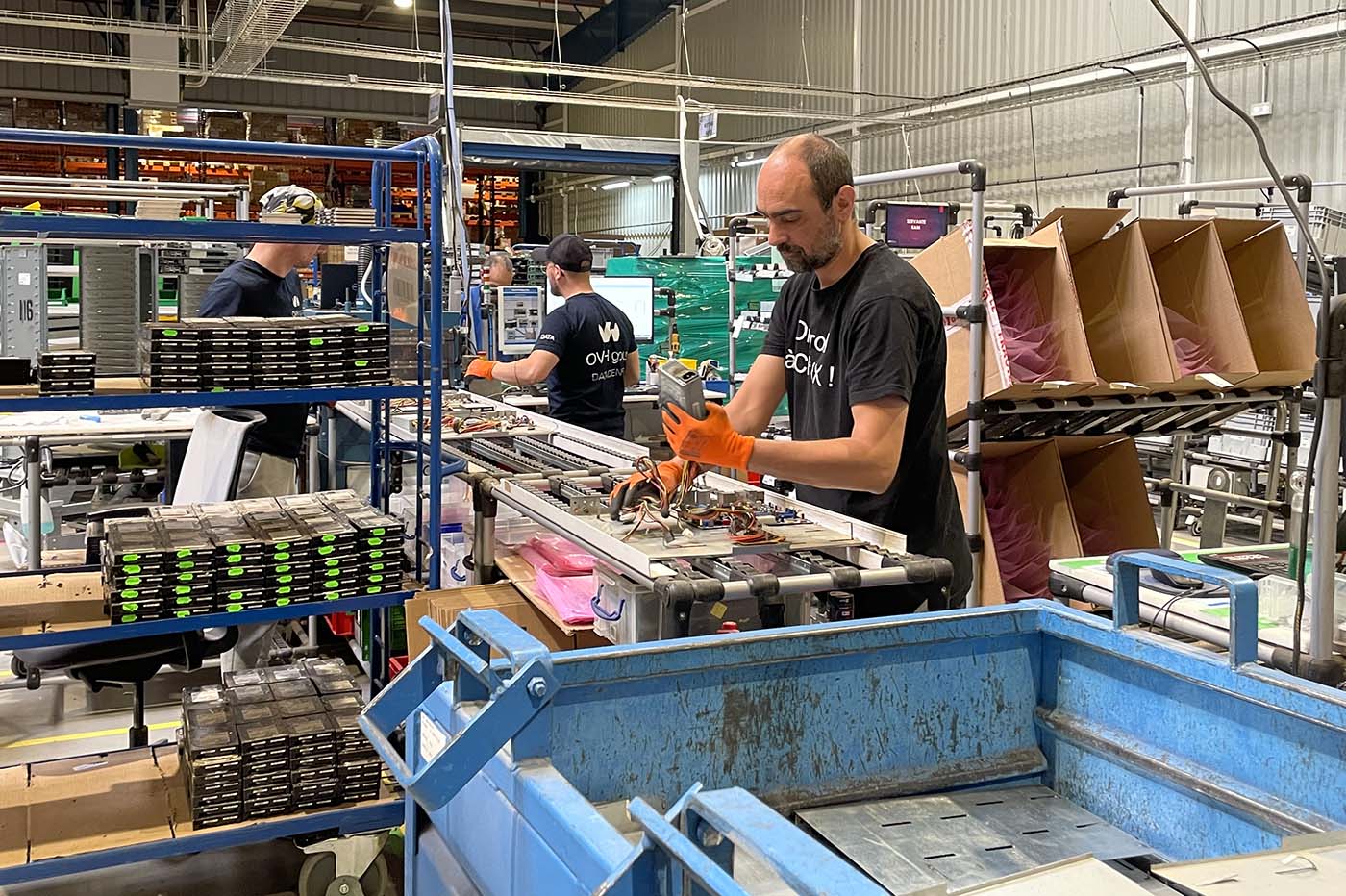
Lorsque le serveur arrive en fin de cycle, il est systématiquement démonté pour récupérer le plus possible de composants et le réintégrer dans le chaîne d’approvisionnement. Il peut s’agir des processeurs, des cartes mères, des barrettes mémoire, des disques durs, ou des alimentations. Les pièces qui ne sont pas utilisables sont revendues à des brokers ou recyclées. En dernier recours, elles peuvent être données, voire jetées dans le cas des câbles ou des châssis métalliques.
« Nous sommes aussi tenus de détruire physiquement quelques disques au hachoir mécanique pour répondre à certaines normes », précise Dominique Michiels.
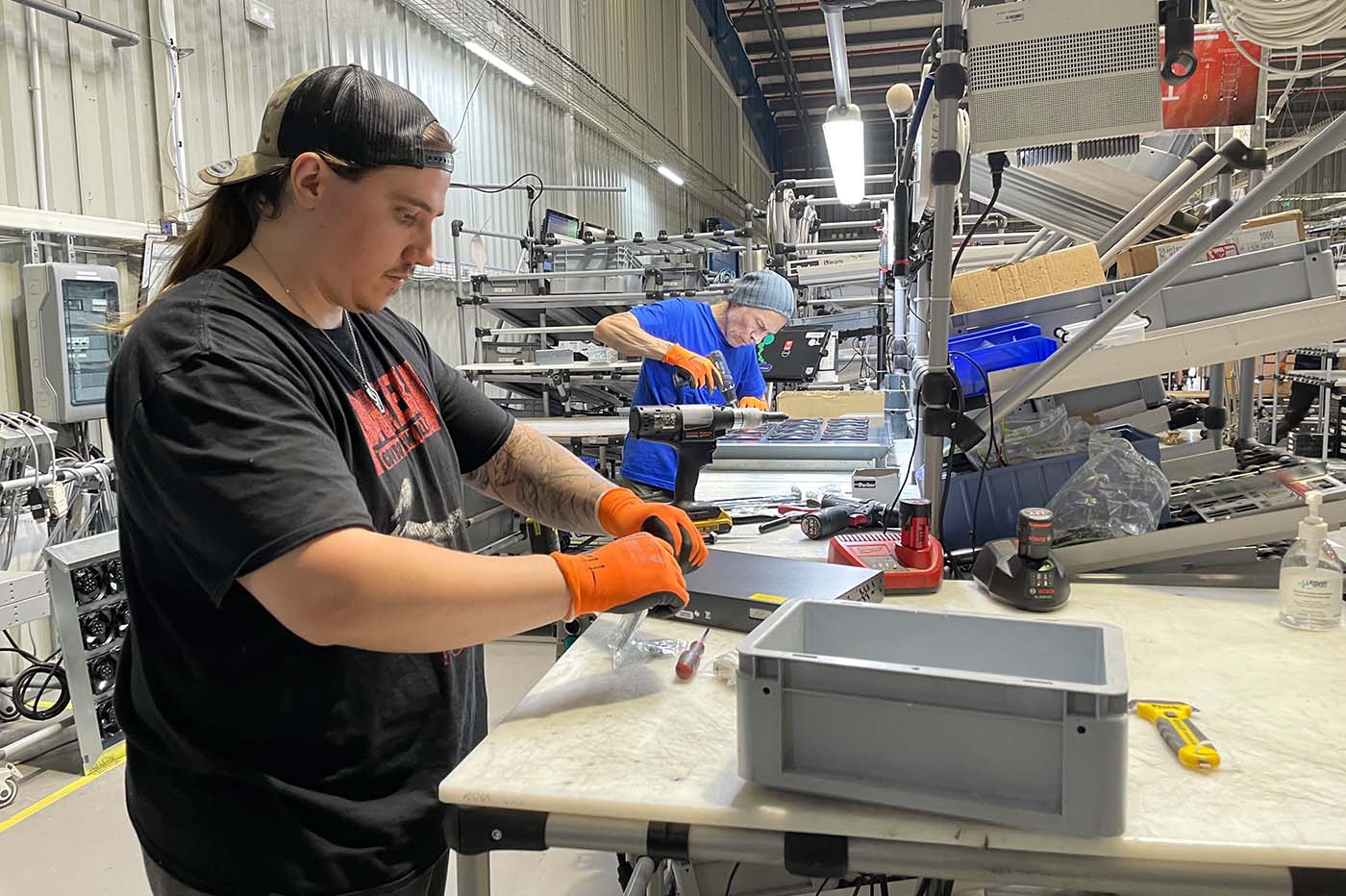
Cette organisation est vertueuse environnementalement, mais on se doute que derrière l’argument « économie circulaire » mis en avant par les porte-paroles de la société, il y a de substantielles économies d’échelle à la clef. Des camions partent en effet toutes les semaines chargés de matériel pour les centres de données d’Allemagne, de Pologne ou du Royaume-Uni. Et ils reviennent chargés à bloc. Des envois par container sont aussi organisés pour desservir les sites hors d’Europe, même si une autre usine plus modeste au Canada est également active.
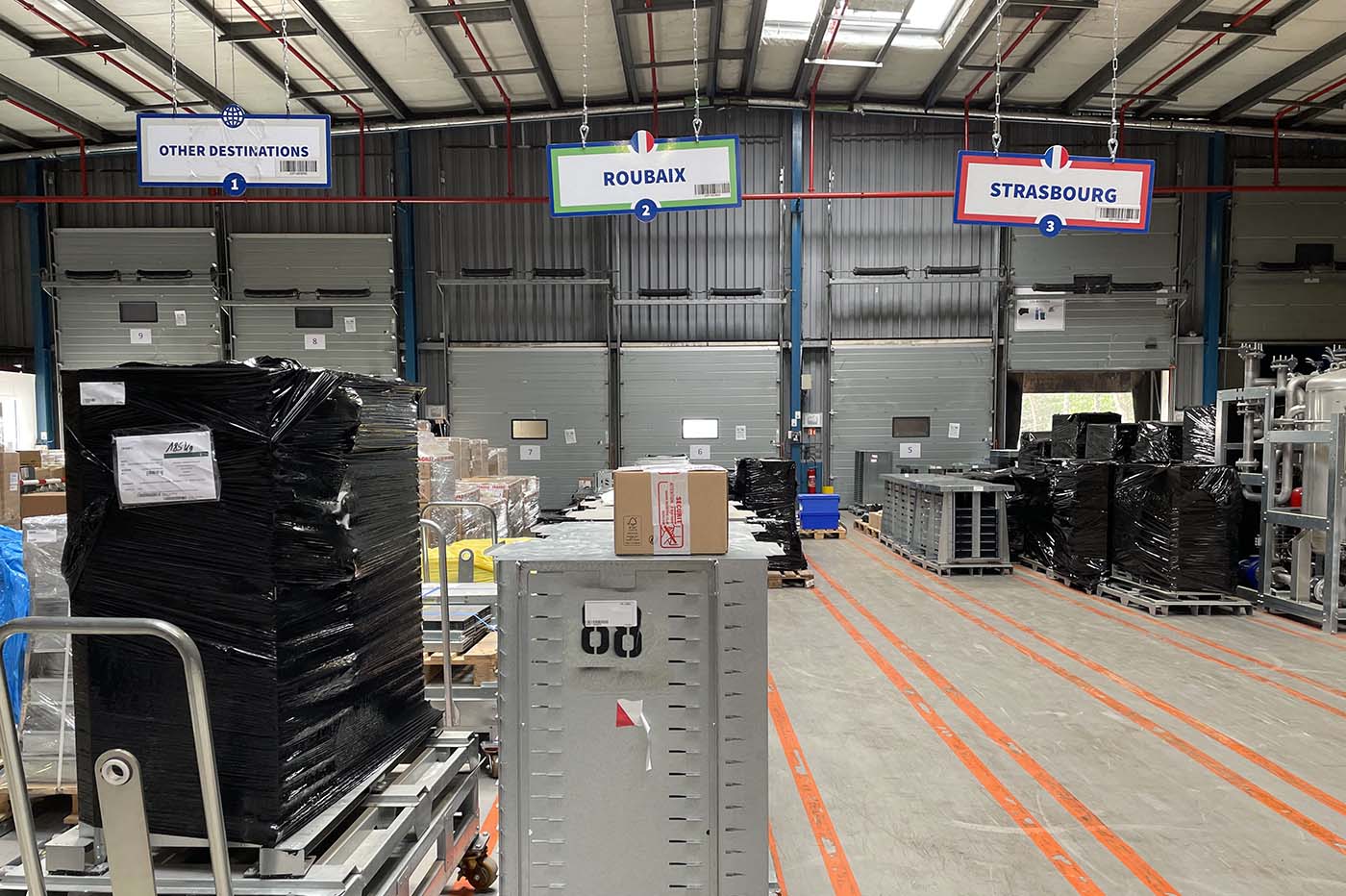
Un design inhabituel
Si l’usine de Croix tient une place aussi centrale au sein d’OVH Cloud, c’est aussi parce que le design des serveurs est très spécifique et que personne d’autre ne pourrait les fournir. Ils sont équipés du fameux procédé de water cooling dûment breveté et inventé par le fondateur de la société, Octave Klaba, et son père Henryk. Une véritable marque de fabrique.

Le principe est de faire circuler de l’eau dans un échangeur directement placé sur le processeur pour le refroidir. « Cela permet d’évacuer 70% de la chaleur du serveur. Les 30% suivant sont traités par air cooling », détaille Guillaume Hochart, directeur Manufacturing de la société. L’air chaud qui reste est en effet aspiré par des moteurs et traité par un échangeur thermique air eau intégré directement dans les baies des serveurs.
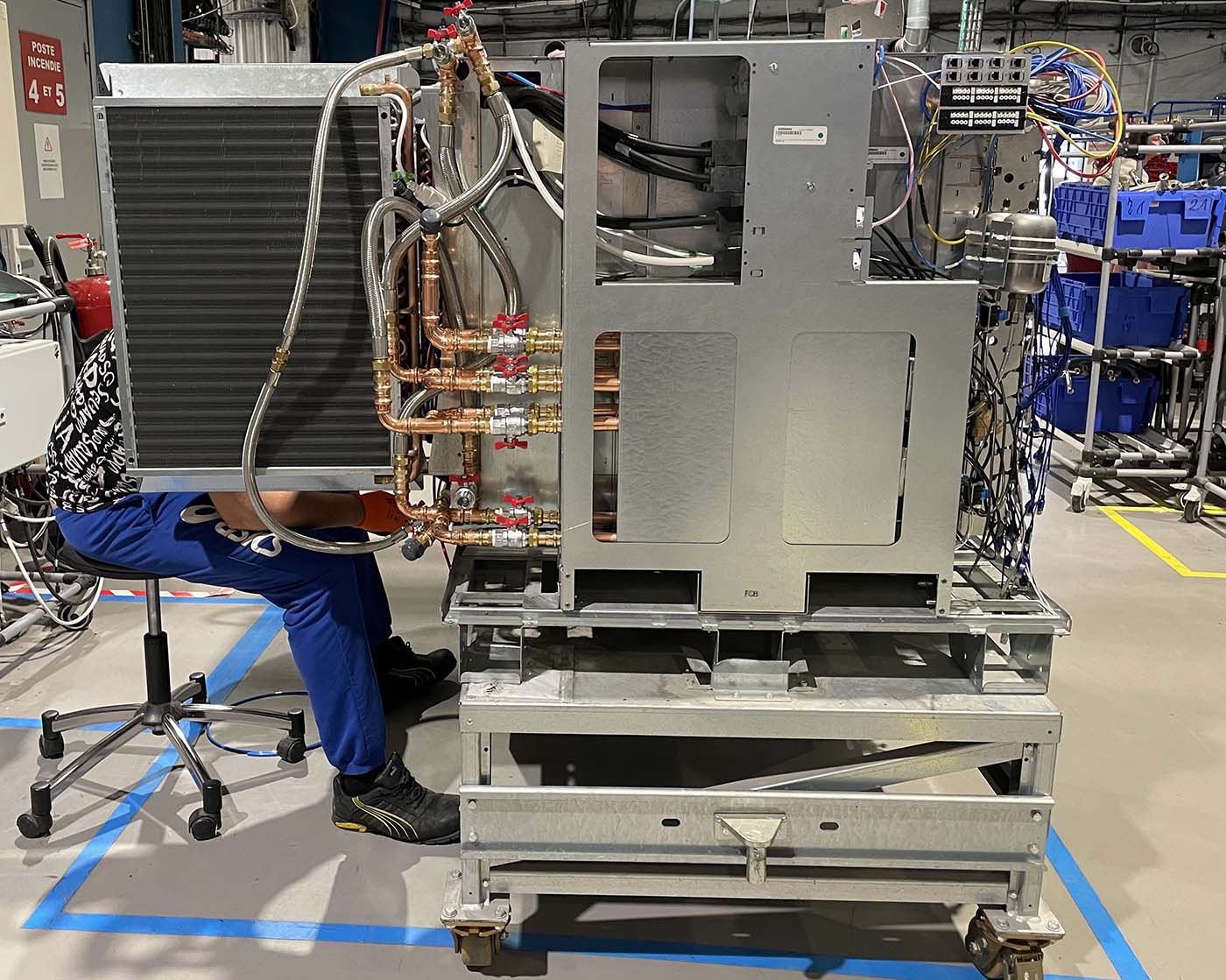
Ce n’est pas la seule particularité de la conception. Il suffit de visiter un data center comme celui de Roubaix 8 pour s’en rendre compte. On est immédiatement frappé par la nudité des installations. Les baies de serveurs ne sont en effet pas intégrées dans des armoires noires comme c’est le cas habituellement. Elles sont disposées dans des « buffets », ce qui donne un effet esthétique un peu brut industriel à l’ensemble. L’avantage, c’est que cela permet de densifier l’espace à l’extrême.

Ce design a peut-être malgré tout rencontré ses premières limites l’année dernière lors de l’incendie de Strasbourg. OVH Cloud a reconnu que les salles serveurs de son data center parti en fumée n’étaient pas compartimentées. Ce qui s’avère très utile dans ce type d’incident pour sauver des serveurs. Depuis, l’entreprise a élaboré un plan “hyper résilience” qui prévoit d’aller au-delà des recommandations des assureurs. Les prochains centres de données qui sortiront de terre comporteront bien des salles compartimentées. Et un nouveau système de protection incendie.